Mobile screw air compressors are widely used and have gradually replaced piston air compressors. The main reason is that the screw air compressor equipment produces air efficiency. Many people will ask what advantages it has that make so many industries choose to use it? Today we will talk about its advantages and working principle.
- High reliability, few compressor parts and no wearing parts, so it operates reliably, has a long service life, and the overhaul distance can reach 40,000 to 80,000;
- Convenient operation and protection, high degree of automation, operators can complete unattended operations without long-term professional training;
- The power balance is good, there is no unbalanced inertia force, it can work smoothly at high speed, and it can complete the work without foundation. It is especially suitable for use as a mobile compressor, with small size, light weight and small footprint;
- Strong adaptability
The screw-type air intake side suction port must be designed so that the compression chamber can fully inhale, while the screw-type compressor does not have an intake and exhaust valve group, and the intake air is only regulated by the opening and closing of a regulating valve. , When the rotor is rolling, the cogging space of the main and auxiliary rotors is large when it turns to the opening of the inlet end wall. At this time, the cogging space of the rotor is communicated with the free air of the air inlet, because the cogging space is exhausted when the air is exhausted. When the exhaust is finished, the tooth groove is in a vacuum state. When it is turned to the air inlet, the outside air is sucked in and flows into the tooth groove of the main and auxiliary rotors in the axial direction. When the air fills the entire tooth groove, the end face of the intake side of the rotor turns away from the air inlet of the casing, and the air between the tooth grooves is closed.
At the end of the suction of the main and auxiliary rotors, the tooth peaks of the main and auxiliary rotors are closed with the casing. At this time, the air is closed in the tooth groove and no longer flows out, that is, [closing process]. The two rotors continue to roll, and the tooth peaks and grooves meet at the suction end, and the matching surface gradually moves to the exhaust end.
During the conveying process, the meshing surface gradually moves to the exhaust end, that is, the gap between the meshing surface and the exhaust port is gradually reduced, the gas in the tooth groove is gradually compressed, and the pressure is increased, which is the [compression process]. During the compression, the lubricating oil is also sprayed into the compression chamber to mix with the chamber air due to the pressure difference.
When the meshing end face of the rotor turns to communicate with the exhaust of the casing, (the pressure of the compressed gas is high at this time) the compressed gas starts to be discharged, until the meshing face of the tooth crest and the tooth groove moves to the exhaust end face, at this time the two rotors The tooth groove space between the meshing surface and the casing exhaust port is zero, that is, the exhaust process is completed. At the same time, the length of the tooth groove between the rotor meshing surface and the air inlet of the casing is longer, and the suction process is again in progress.
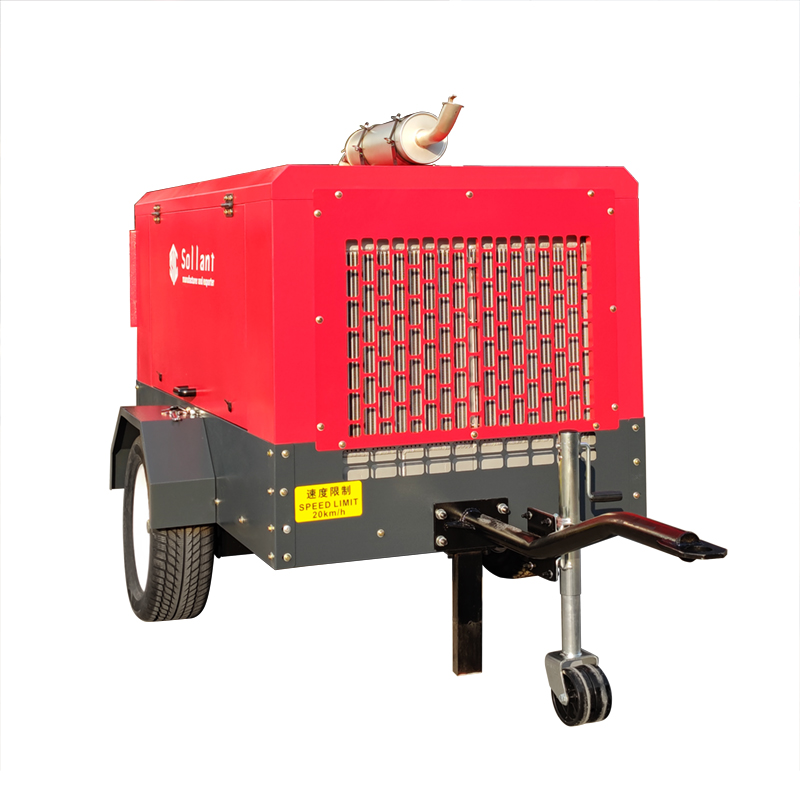
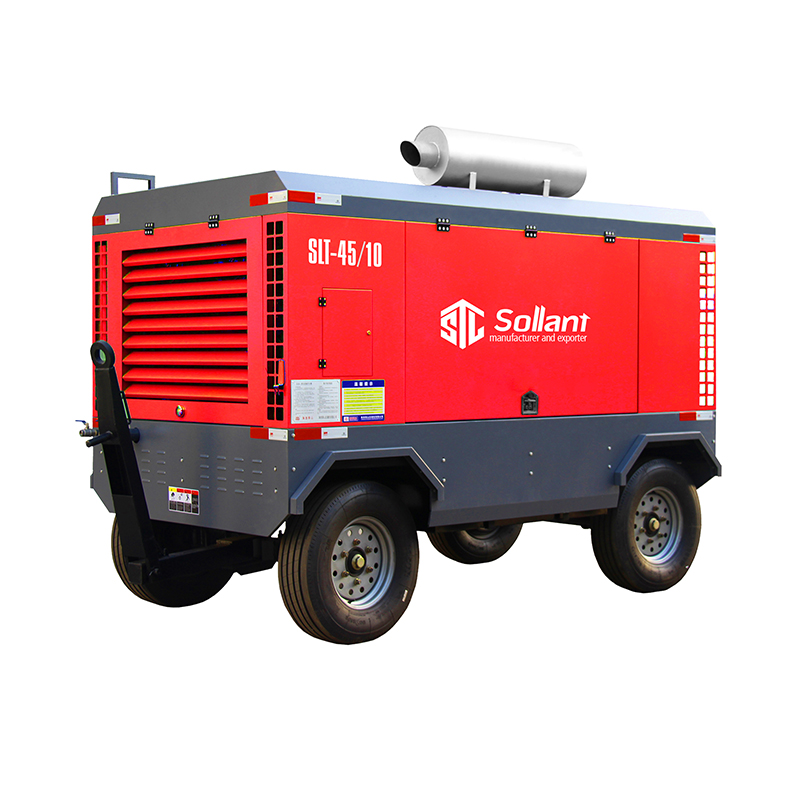
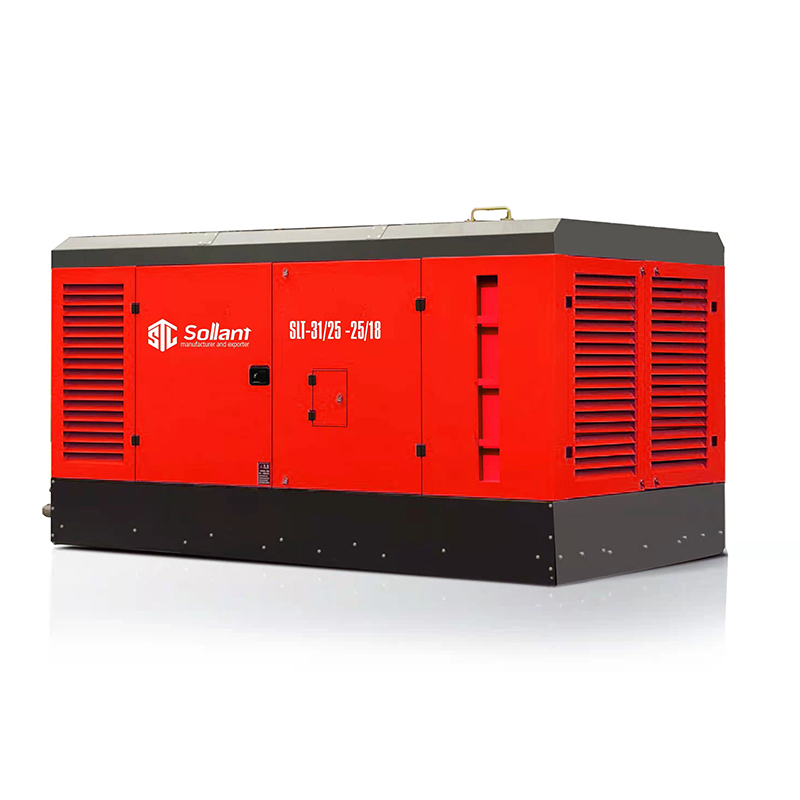